Bentonite to Polymer Slurry, the Sustainable Route to Building Reinforced Concrete Diaphragm Walls
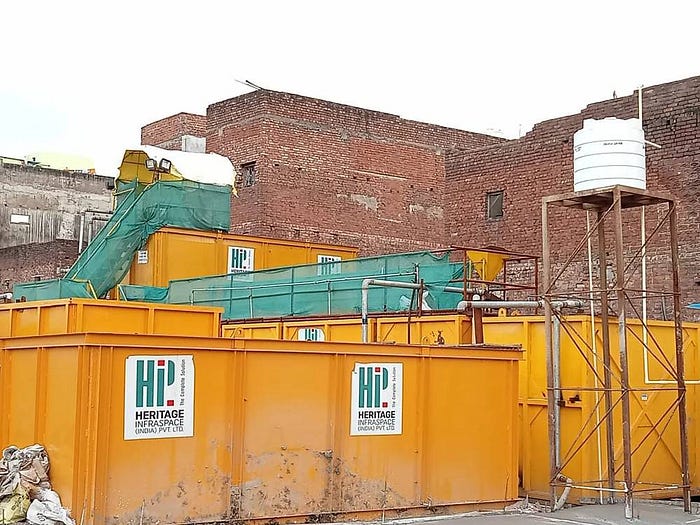
Bentonite has been a crucial construction element in building reinforced concrete diaphragm walls for deep basement structures. But over the years, civil construction companies have started using polymer in their excavation fluids and slurry.
Read on to understand the importance of both the materials in constructing concrete diaphragm walls, the differences between them, and how polymer is growing as a more sustainable option in excavation activity while bentonite remains the foolproof back plan for civil engineers.
What are Bentonite and Polymer Slurries?
Bentonite clay is formed by the alteration and weathering of volcanic ash and is abundant in the clay mineral montmorillonite, which swells when mixed with water and possesses exchangeable irons on the surface that produce thixotropic suspensions. Typically mined in Rajasthan India, it is extensively used in diaphragm wall construction as an excavation fluid. Bentonite clay (in powder form) is combined with water in a colloidal mixer where the clay particles bond with one another to form a gel-like texture.

The mixing process continues till the standard quality is achieved for the slurry.
Polymer slurry is prepared with the combination of water and hydrophilic superabsorbent polymers like polyethylene glycol, polyvinyl alcohol, or carboxymethylcellulose to form a thick, viscous mix. These water-soluble polymers have been used to stabilise deep excavations for reinforced concrete diaphragm wall trenches. When compared with conventional bentonite slurries,this engineered fluid is known to offer a variety of advantages including smaller site footprint and lesser environmental impact.
How is a bentonite slurry or polymer slurry prepared?
The slurry is prepared with the aim of attaining maximum hydration of bentonite clay or polymers. Hence, it must be slowly added into the mixing water to ensure all particles are irrigated and do not get lumped. Potable fresh water should be used in the mixing process to obtain the best results. Alongside this a chemical analysis, as listed out by the Indian Standard Code of Practice for Construction of Diaphragm Wall, must be conducted to ascertain the suitability of water. If needed, chemical treatment is given to the water before its usage.
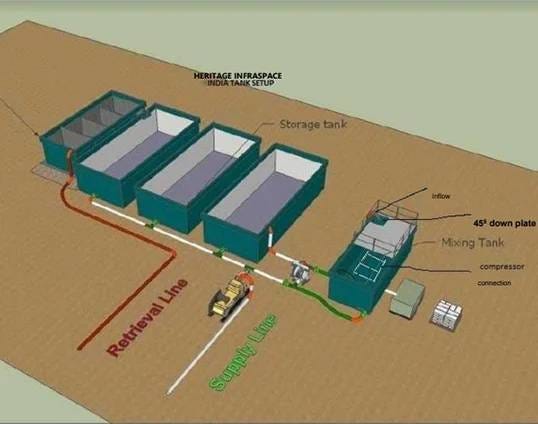
The preparation of the slurry is done either in batches or in a continuous process, depending on the type of equipment used. The components are added in a high shear mixer through a simple venturi-hopper. To assure the dispersion of all the individual particles in the mixing water, the mixing equipment must generate sufficient shear. Once prepared, it is moved to storage tanks, and from there they are supplied to the excavation point, to be filled into the cavity of the soil. This entire process, including the testing is done on-site by the civil construction company assigned to build the diaphragm wall.